Tin is a metal with a discreet yet soft and beautiful silvery shine.
It has a long history and has been widely known since BC, and was once as valuable as gold and silver.
In Japan, it has long been used as Sake and tea vessels to mellow water and Sake, and in modern times it is used to make a wide range of small items such as flower vases and cutlery.
In this article, the history of tin in Japan and its characteristics will be unravelled.
Tin has long been a favourite.
Tin treasures are preserved in the Shosoin Repository in Nara prefecture.
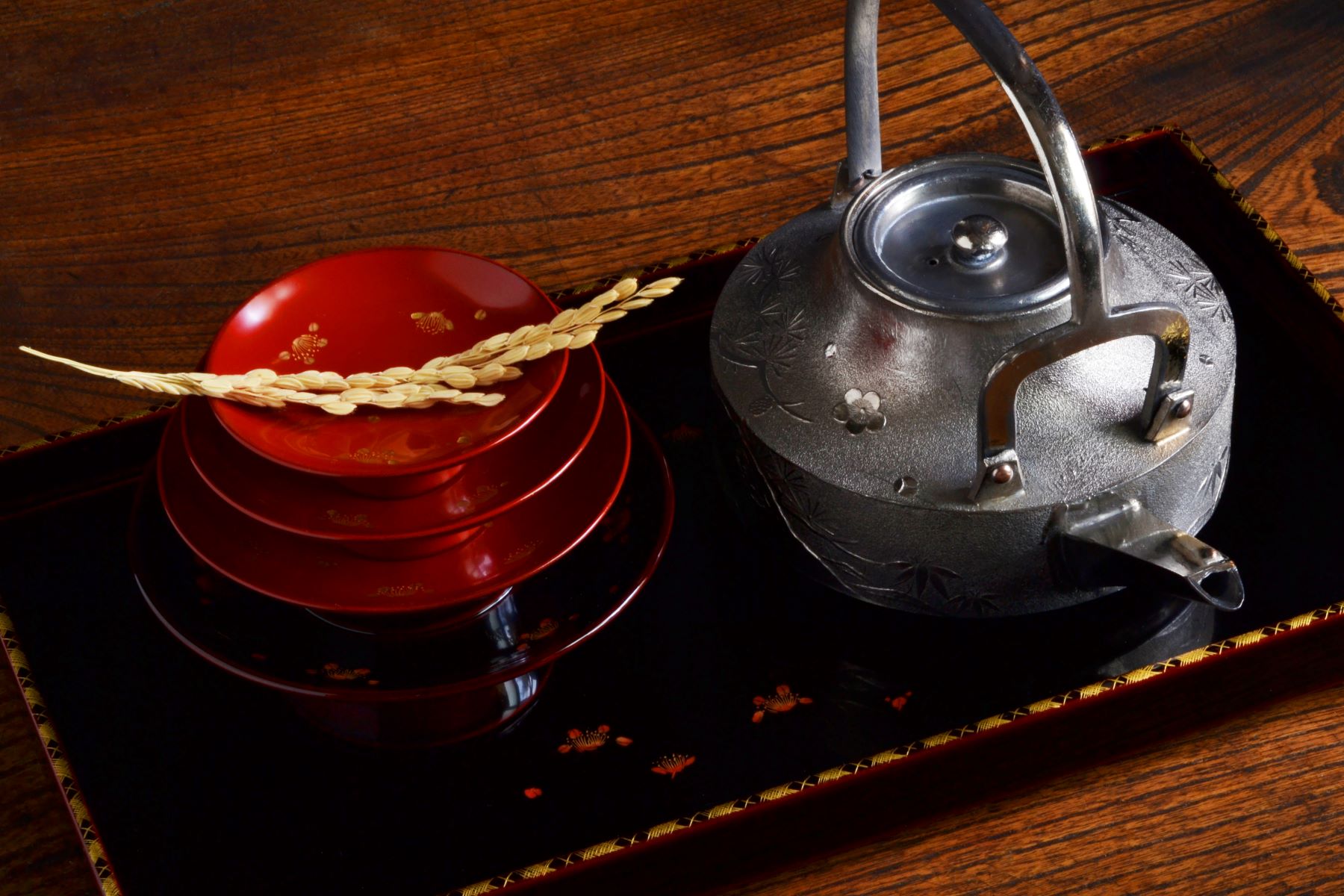
Tin is not a natural raw material, but a metal refined from a mineral called 'tinstone'.
Since ancient times, it has been used as a raw material for bronze in many parts of the world and was once actively mined in Japan.
There are various theories as to when tin was introduced to Japan, but the earliest known date is around the 6th-7th century, and tin necklaces and bangles have been unearthed as burial accessories in ancient tombs, suggesting that it was used as an ornament and craft. It is also thought to have been used as a vessel during the Asuka and Nara periods, several tin medicine jars and water bottles are preserved as treasures in the Nara Shosoin.
In the past, tinware was a luxury item on a par with gold and silver and was used for sacred objects such as Sake and tea utensils used at court, Sake cups and Sakakitate at shrines. Even today, the Sake cups into which sacred Sake is poured are called 'suzu', and it is customary to call Sake 'osuzu' in the court.
It was not until the late Edo period (1603-1868) that tin became a part of the daily life of the public. Osaka prefecture is said to have flourished as a major production centre, and from the Taisho to the early Showa period a large number of craftsmen called tinsmiths were active.
Eventually, with the outbreak of World War II, production had to be curtailed as munitions controls made it difficult to obtain tin and more craftsmen were called up.
However, tinware techniques and skills are still handed down in various regions, and in 1983 (Showa 58) 'Osaka Naniwa Tinware' was designated and approved as a traditional craft.
In addition to making the water inside taste better, it is also safer.
The main characteristic of tin is that it is softer than other metals and does not crack. Tin, which is 100% pure, can be bent freely by hand, and some products are made using this peculiarity.
It is a very special type of metal, resistant to rust in air and water, and although not scientifically understood, it is said to absorb impurities in the liquid it contains and mellow the taste.
The fact that it is non-toxic and has no metallic odour is probably the reason why it has been popular as drinking and tea utensils since ancient times.
It is also said that flowers arranged in tin vases last longer because the water in the tin is resistant to decay due to its antibacterial properties.
You might think that it would be difficult to care for a product that is 'designated as a traditional craft', but it's relatively simple.
Note that it is weak against acidity and alkalinity, soft and easily damaged, so it should be washed gently with a soft sponge and a mild detergent after use.
If the lustre becomes dull, polish with baking soda dissolved in water to restore the gentle silver colour unique to tin.
As the melting point is low at approximately 270°C, it should not be placed near fire & avoid using open flames, and it should not be stored in the freezer as it may be altered at very low temperatures.
Various techniques are used to make use of the softness.
Although different workshops and makers use different methods and techniques, tinware production methods can be divided into three main categories: casting, grinding (rokuro-hiki) and hammering (forging).
In 'casting', liquid melted tin is poured into moulds (casts) made of cement, sand or metal using a ladle.
Great care is taken to keep the moulds at the right temperature, as tin hardens quickly if the temperature is too low.
Once the tin poured into the mould has cooled, it is gently removed to avoid scratching it, and any protrusions (burrs) created during the moulding process are scraped away.
The 'hikimono' method involves mounting the tin moulded by casting on a wheel and shaving it with a planer or similar tool.
For items such as tea caddies, in which the casing mouth and lid are combined, or for items such as teapots, which cannot be cast in one piece, the upper and lower parts are made separately and finished by joining them together (firing together).
Smaller parts such as the handle and spout of a teapot are joined using a metal (wax material) as an adhesive (brazing), which melts at a lower temperature than tin.
In addition to mirror-finishing by polishing, there are also techniques such as tsuchime, in which the surface is hammered to create a pattern, and painting and colouring to add a glamorous finish.
Uchimono (forging) is a technique in which tin is cast into a sheet shape and then hammered out with a hammer or mallet to create a three-dimensional finish by hand.
The surface is tapped (tsuchime) using various hammers and hammers to create a unique pattern-like unevenness on the surface.
Because of its soft and easily damaged nature, tinware is more difficult to process than other metals and requires a high level of skill, regardless of the production method or technique used.
The slightest difference in angle or force can affect the finished product, so the craftspeople say they cannot let up in every step of the process.
Summary
Tin is also characterised by its good thermal conductivity, so if you pour cold Sake into it, the entire vessel will cool down and remain at the same temperature for a long time. It also mellows the mouthfeel and makes ordinary Sake taste special.
This summer, why not enjoy cold Sake in tin Sake cups?